
Capital Equipment, a diversified construction company located in Missouri, manages hundreds of assets across the United States. Unfortunately, the maintenance management program the company was using didn’t provide the actionable insights they needed to keep track of the health of their equipment or prevent failures from happening in the first place.
As a result, Capital Equipment had a number of “unavailable” assets at any given time—a situation that they considered unacceptable and untenable. They understood they could be doing better but needed support to get started.
Capital Equipment turned to its local Mobil™ lubricants distributor Wallis Lubricants for assistance. Working with the experts at Wallis and the Missouri-based Mobil engineer, Capital Equipment built out a tailored comprehensive preventative maintenance and oil analysis program that was designed for their needs.
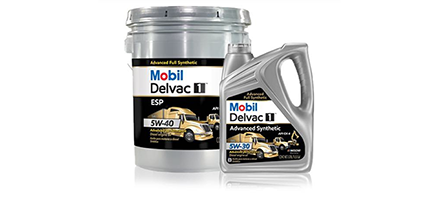
When Capital Equipment implemented the maintenance and Mobil Lubricant Analysis program, the benefits were almost immediate. Mobil’s oil analysis program identified troubling engine conditions in one of their Sandvik drills. All signs pointed to a pending premature failure. Capital Equipment moved quickly to address the engine conditions and avoided a costly two-week repair that a complete equipment failure would have required.
Beyond preventing that engine failure, Capital Equipment’s preventative maintenance and Mobil Serv℠ Lubricant Analysis program has led to other benefits as well. The company was able to:
- Double oil drain intervals from 250 to 500 hours
- Free up 96 hours of maintenance technician time
- Reduce oil waste by 4,680 gallons
- Extend time between equipment preventative maintenance, allowing them to increase their productivity and get the job done on time.
In 2020 alone, Capital Equipment estimated that the program saved the company $497,000.
“As they continue with the program going forward, the financial benefits are just going to continue to compound over time and as they continue to grow their business,” said Adam. “If they weren’t believers before that ‘an ounce of prevention is worth a pound of cure,’ they certainly are today.”
Related content
* This Proof of Performance is based on the experience of a single customer. Actual results can vary depending upon the type of equipment used and its maintenance, operating conditions and environment, and any prior lubricant used.