Jim Hannon, Industrial Lubricants Technical Advisor, ExxonMobil Research and Engineering
A common problem that operators in the power industry consistently face is the formation of varnish. Varnish has historically been used as a catchall term for oil deposits, but specifically refers to the hard, oil-insoluble organic residue that cannot be easily removed from mechanical components by wiping away.
Varnish and sludge, the soft, pliable, organic residue that can be easily removed from components, form in different ways and there are many factors that contribute to their formation. Here are the three main mechanisms of varnish formation:
- Thermal degradation of oil which can take place at temperatures above 300°C
- Oxidation, a reaction that causes decomposition of the oil
- Contamination of the oil, through either internal or external sources
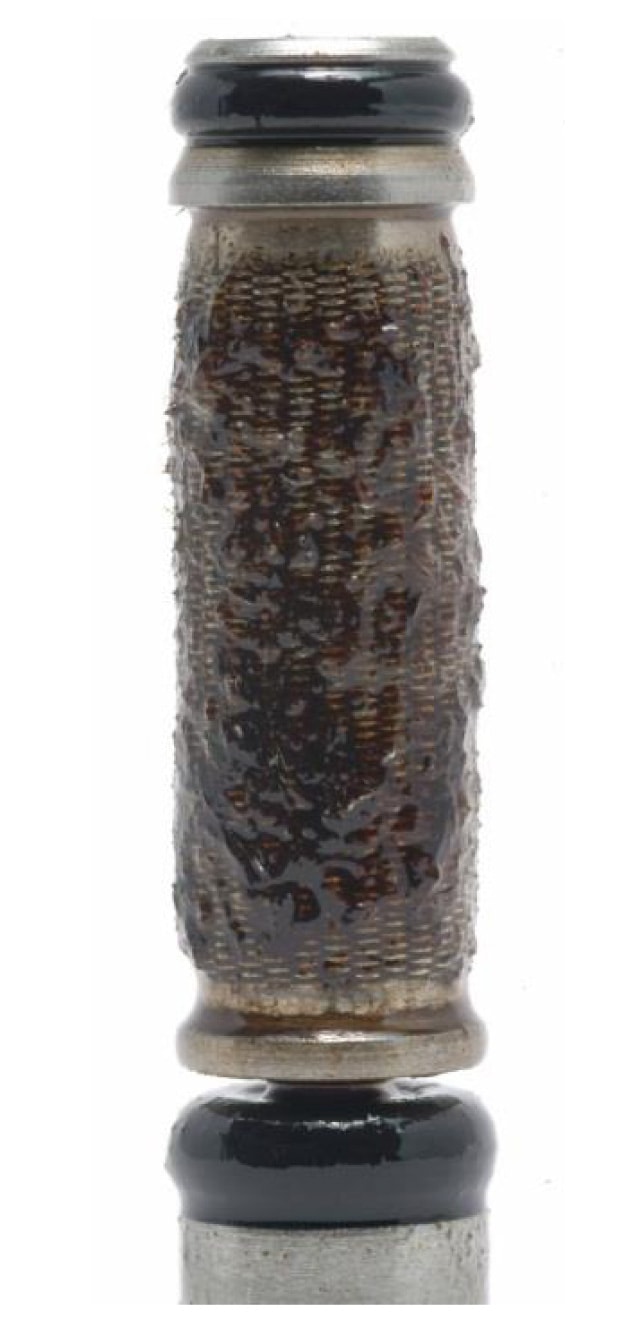
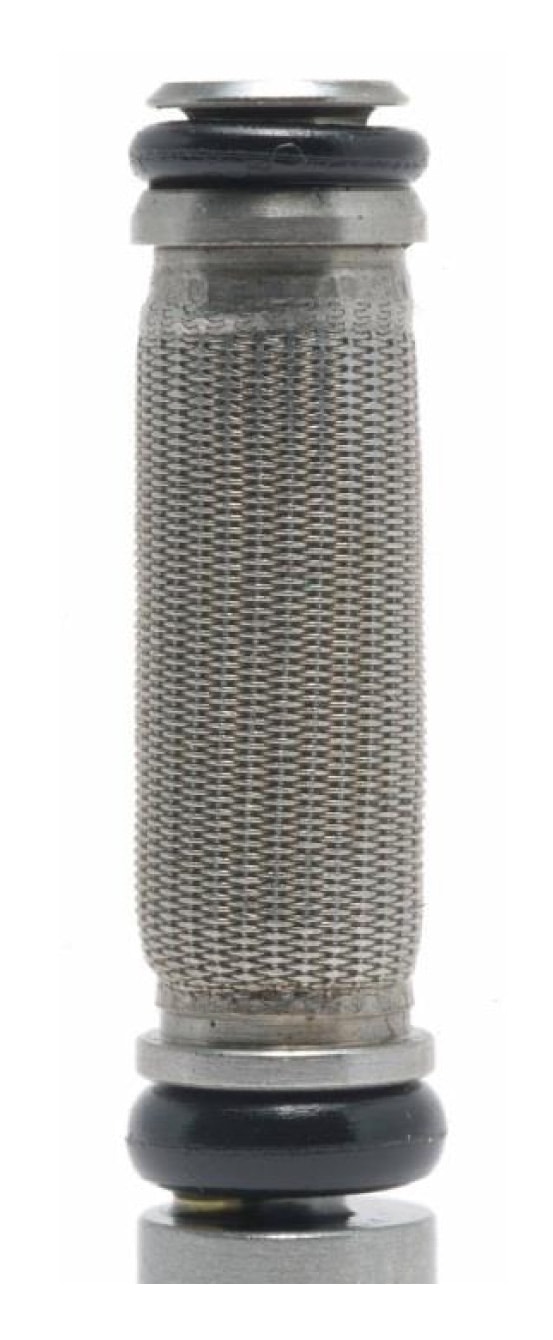
Comparison of a servo valve filter with varnish/sludge to a new filter.
According to an ExxonMobil Fuels & Lubricants survey of 192 gas turbine power plants, running a combined 626 gas turbines, approximately 40 percent of turbine operators report current or historical issues with oil varnish within the first six years of service.
Turbines with common hydraulic and bearing reservoirs are far more susceptible to unit trips or no-starts related to varnish than turbines with segregated reservoirs. Additionally, mild varnish can accumulate on journal and thrust bearings with little to no impact on bearing temperatures or shaft rotations. For this reason, early oil varnish detection and prevention is incredibly important for common hydraulic/turbine reservoirs, compared to turbines with separate hydraulic and turbine reservoirs.
Mild varnish can build up on journal and thrust bearings with little or no impact on bearing temperatures or shaft rotations, and unit trips or no-starts are rarely, if ever, reported due to varnish in turbine bearings. For this reason, I want to stress that practices to encourage varnish detection and prevention should focus on turbines with common hydraulic and turbine oil reservoirs.
Varnish theory
While treating the symptoms of varnish with mitigation technologies may extend service life, for reliable operation it is important to begin with a clean system and use turbine oil designed to prevent varnish from forming. A well-balanced formulation that utilizes high-performance base stocks and advanced technology additives will be your first line of defense against the formation of sludge and varnish. In general, higher-quality base stocks blended with advanced technology additives offer the best protection against varnish.
There are additional details you should consider when selecting a well-balanced gas turbine lubricant.
The first area of consideration is the turbine oil’s ability to control deposits. Some oils generate more deposits than others, but choosing an advanced turbine oil, formulated to limit the generation of sludge and varnish and keep deposits in suspension, will greatly reduce the risk of varnish formation.
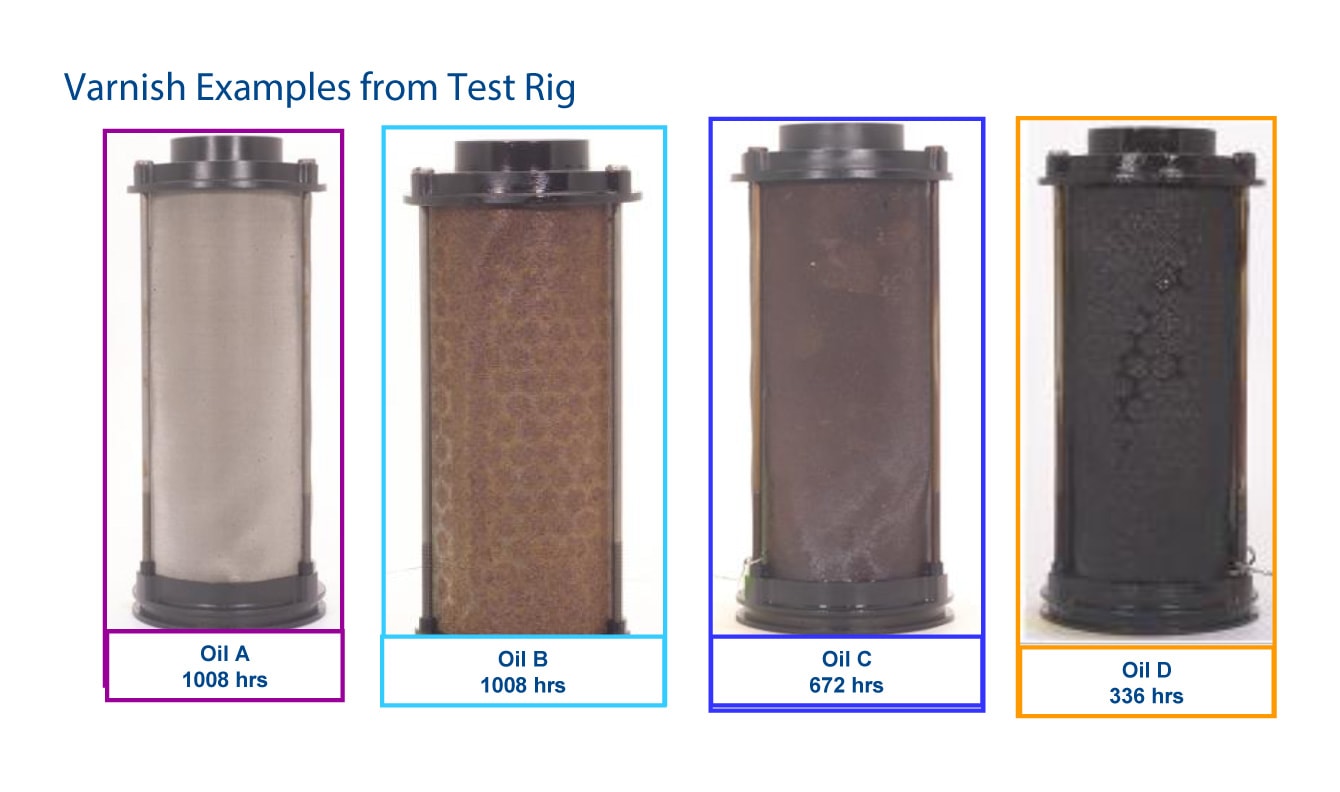
The above photos show varnish formation of four commercially available oils.
The second area to consider is an oil’s oxidation stability. Turbine bearing temperatures approaching 120°C, in combination with equipment metallurgy, contaminants and entrained air, contribute to the oxidation process that precedes the formation of varnish. To combat this reaction, opt for lubricants that feature higher-quality turbine oil base stocks, and carefully selected additives and antioxidants. Next, consider air release and foam control.
In an oil with poor air release performance, entrained air can be compressed in turbine bearings or high pressure hydraulics, which will cause adiabatic compression (a.k.a. micro dieseling). Adiabatic compression can cause localized high oil temperatures, which may facilitate the formation of varnish.
Excessive surface-level foaming also can accelerate oxidation and lead to operational issues, such as the inability to properly measure lubricant levels or oil reservoir overflow. Oils formulated to promote rapid air release and minimal foam formation will provide superior protection against the formation of varnish.
Filterability of a fluid, or the ability to pass through a filter with minimal pressure drop, is another performance consideration that will contribute to oil filter varnish formation. Oils with poor filterability will load filters faster that those with good filterability, which often translates into more frequent filter changes.
You should next consider anti-rust and corrosion protection, as rust and corrosion can also contribute to oxidation and the formation of contaminant-based varnish. For this reason, you should look for oils formulated to minimize rust and corrosion.
Finally, consider the oil’s ability to protect against wear.
Wear on high pressure hydraulic components, gears of the accessory gearbox, generator reduction gear or turning gear can directly impact gas turbine performance. Wear material from these components be an indirect source of varnish formation, as the wear metals can act as an oxidation catalyst.