Tom Schiff, Global Field Engineering Support Manager, ExxonMobil Fuels and Lubricants
Each year, Plant Engineering – an industrial manufacturing outlet – surveys a number of engineers and maintenance professionals to get a sense of overall maintenance strategies in the United States.
This year, the Plant Engineering Maintenance Study revealed a promising outlook for maintenance practices, with 31 percent of respondents reporting that they have implemented preventative maintenance programs in order to reduce instances of unscheduled downtime, and just fewer than 50 percent reporting that they have implemented some form of predictive maintenance program at their facilities.
However, the survey found that 57 percent of respondents still report resorting to reactive maintenance procedures in their operations. This is an unfortunate, short-term strategy, which can lead to costly equipment repair and replacement.
In fact, those surveyed even recognized the pitfalls of a reactive maintenance program, noting that, as compared to planned and predictive maintenance programs, reactive maintenance does not provide advantages with regard to safety, cost effectiveness, downtime or energy savings.
Q: What are the advantages to the maintenance strategy/strategies in place at your plant? (n=283)
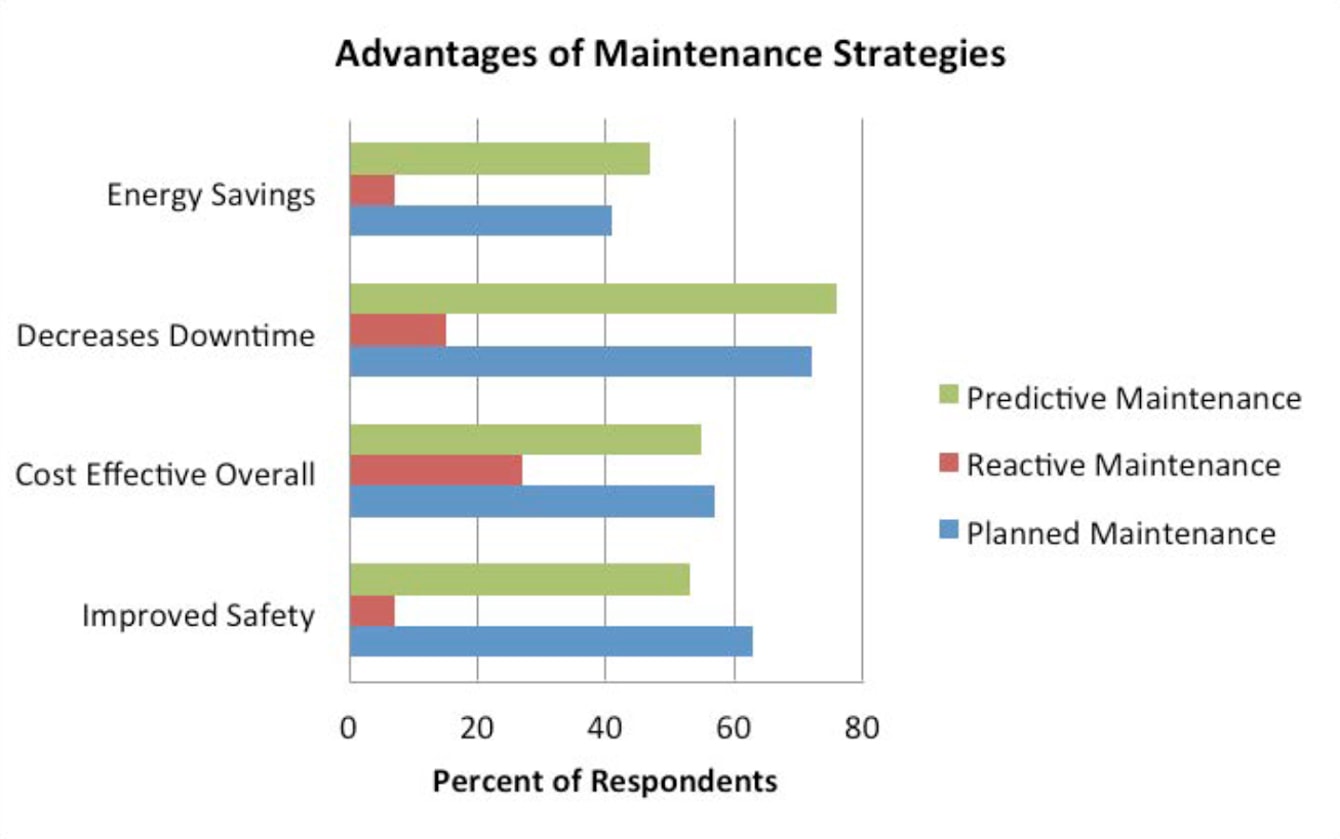
Source: Plant Engineering 2014
By implementing a preventive or predictive maintenance program, maintenance professionals can take a proactive, long-term view with regard to routine maintenance. With this approach, operators will be able to facilitate key improvements in safety, productivity and environmental care. To help strengthen preventive maintenance programs at your facility, consider implementing a comprehensive oil analysis program.
Start with the oil
One of the most cost-effective places to start is with a comprehensive oil analysis program. By testing the condition of in-service lubricants and internal hardware, companies can identify contamination and wear before they reach “alert levels.” This will minimize unscheduled maintenance and extend equipment life.
At the core of the program, technicians should take representative in-service lubricant samples on a regular basis. The frequency should depend on the equipment criticality and the failure modes encountered. The frequency can range from on line with sensors to monthly, quarterly and sometimes longer for off-site laboratory samples. Samples should be taken from critical components in the plant such as gearboxes, pumps, fans and compressors.
Technicians should look for wear metals, contaminant elements and additive elements in the oil. Strains such as high operating speeds, high pressures and high temperatures can impact productivity. Dirt and other insoluble particles can contaminate machinery.
It is critical to monitor water content, which can destabilize lubricants and increase corrosion. Water can seep in through condensation, wash-down or cooler leaks. Also, watch out for viscosity fluctuations or changes in the lubricant’s resistance to flow.
In need of valued partners
Unfortunately, with companies looking to cut costs, maintenance managers are often left wondering where they will receive the funds to step up preventive and predictive programs.
While managers can begin with a little online sleuthing and pull case studies showing the money saved by other companies through maintenance, it’s imperative for lubricant suppliers – like ExxonMobil and leading equipment manufacturers – to continually work with industrial operators to enhance understanding of the value of proactive maintenance, and most importantly, how to implement the plan.
These effective collaborations will create a compelling case for expanding maintenance programs, or at least preventing those existing from being cut, and foster true business partnerships that can deliver exceptional support and value to industrial operators.