Roberto Montes de Oca, Americas Technical Help Desk Engineer, ExxonMobil Research and Engineering
I am often asked what causes sudden changes in the physical or chemical properties of a lubricant, or the appearance of wear metals in used oil analysis reports. Let me share some insights on this topic.
Often, when operators receive normal results in used oil analysis reports, they think it’s a sign that all is well and simply save the results and move on. Receiving normal results is great news, but it serves no purpose if operators pass over the opportunity to take a closer look.
It’s important to remember that the purpose of a comprehensive oil analysis program is to provide ongoing insights into lubricant and equipment performance. This data trends to be thoroughly analyzed and, done right, can help operators identify potential areas of concern for key equipment where corrective actions can be most impactful.
Paying attention to normal analysis results is necessary to identify in advance when abnormal conditions arise, understanding that such conditions could lead to premature component damage or even catastrophic failures if not addressed in time.
When you receive normal results, take a moment to compare within the previous report to identify any changes in the oil’s physical or chemical condition.
For example, an increase in oil viscosity could signify that the system has started to run at higher temperatures than normal or that the application is overloaded, even if the increase in oil viscosity has not reached the limit for your application. The reason for changes in viscosity can vary, but to prevent potential damage, the reason needs to be identified and corrected as soon as possible.
Similar situations can occur with wear metals. For example, if you notice higher values of copper in your oil analysis results, along with a change in the oil viscosity, you might want to review the machine cooling system to monitor pipe condition, search for loose fittings and identify any unwarranted vibrations.
Common abnormal conditions that arise include diesel engines showing increased levels of silicon and iron, but failing to reach oil analysis alarm limits; or hydraulic oil analysis results showing an increase in water and copper, which can be a precursor of a future pump or valve failure.
Of course, if you see a sudden increase in any value, it could be due to an oversight in the findings of previous oil analysis results.
Will that always be the case? No. We still need to consider that many external factors can lead to unexpected damage. However, following a disciplined oil analysis program can help to anticipate situations that will help make operational failures the exception, not the rule.
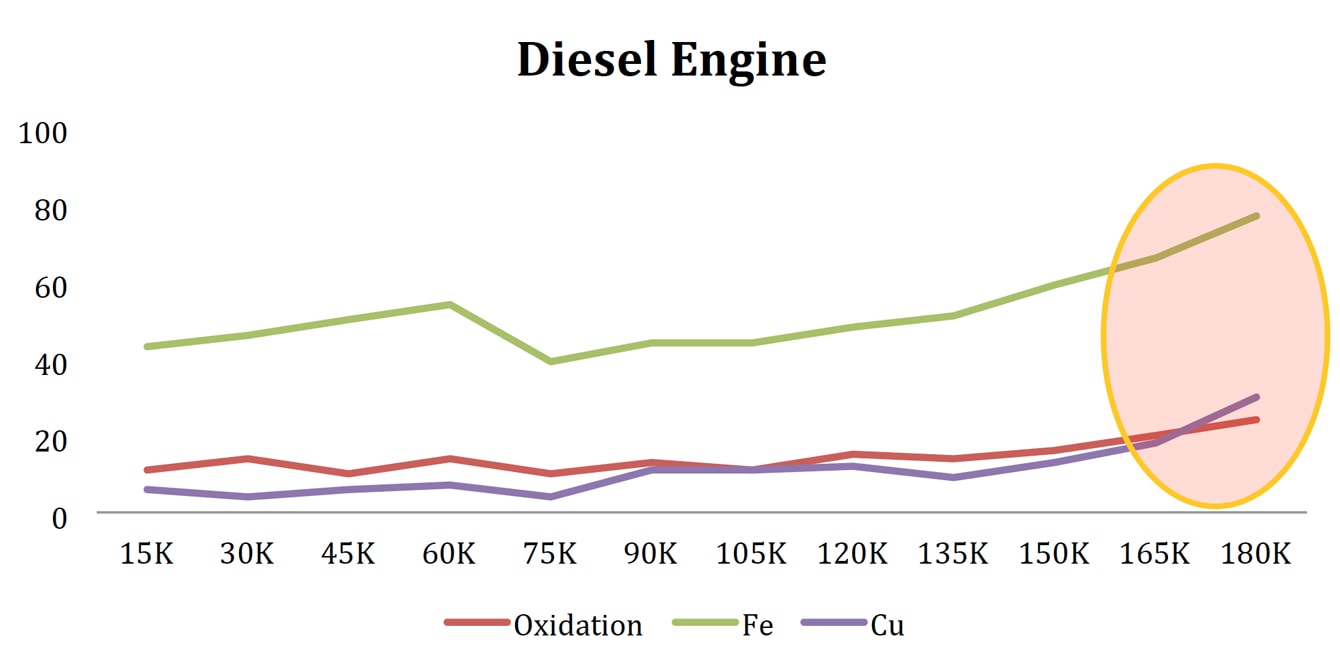