Mobil SHC™ synthetic grease helps to eliminate bearing failures and improve production output
Maintenance costs
decreased by up to 200%*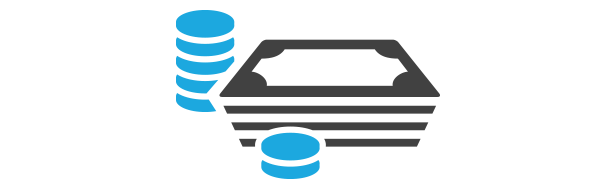
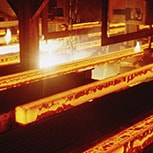
Situation
A competitor’s conventional grease was used for two years to lubricate thrust bearings valued at US $21,000 in the thrust regulating mechanism of a piercing mill «450». The equipment worked at full capacity nonstop, and was exposed to axial loads as high as 350 tons. Initially, the thrust bearing grease was automatically replenished at a rate of 250 g/hour, however, following bearing failures the feed rate was increased to 500 g/hour.
While this improved equipment performance, the wear of rollers and bearing retainers was not prevented. Five bearings had been replaced, resulting in a total of 32 hours unscheduled downtime and a production loss of 1,600 tons of tubes. This also resulted in more regular maintenance inspections — once every two months.
Recommendation
The ExxonMobil field Lubrication Field Engineer recommended a low NLGI class synthetic grease, Mobilith SHC™ 007, with a higher penetration value. Its outstanding high temperature characteristics give it higher stability, while its excellent structural stability combined with a special additive combination provide necessary long-term equipment protection.
Result
The switch to Mobilith SHC™ 007 synthetic grease has proven to be successful. The initial grease feed rate of three times per work shift was reduced to once per shift, reducing the total grease consumption from 0.6 to 0.1 tons per month. Furthermore, the customer has managed to significantly cut costs thanks to:
- Elimination of bearing failures
- No grease related unscheduled downtime
- Longevity of bearings increased from 3 to 17 months
- Regular maintenance inspections increased from 2 to 4 months
*This proof of performance is based on the experience of a single customer. Actual results can vary depending upon the type of equipment used and its maintenance, operating conditions and environment, and any prior lubricant used.